Just How Professional Packaging Equipment Fixing Services Decrease Downtime and Increase Performance
Specialist packaging device repair service solutions are vital in reducing downtime and enhancing efficiency through specialized diagnostics and prompt treatments. The ramifications of such services extend past instant repairs-- unpacking the broader effect on functional performance exposes critical insights right into long-term performance approaches - packaging machine repair service.
Relevance of Timely Fixes
Prompt repair services of packaging makers are vital for maintaining functional effectiveness in any type of manufacturing atmosphere. When equipment breakdowns or breaks down, it can cause significant disturbances in assembly line, causing raised downtime and shed profits. The longer a product packaging equipment stays out of order, the better the effect on general performance, possibly triggering hold-ups in fulfilling orders and diminishing client satisfaction.
In enhancement to the instant economic ramifications, delayed fixings can lead to extra substantial damages to the machinery. Elements that are not resolved promptly can degrade better, requiring even more costly repair work or total substitutes, which might have been avoided through prompt intervention. Additionally, regular maintenance and punctual fixings can improve the life-span of product packaging devices, ensuring that they operate at ideal efficiency levels.
Spending in expert product packaging device repair service services is essential for alleviating these dangers. An aggressive approach to repair services not only keeps manufacturing routines but likewise cultivates a society of reliability within the organization. By prioritizing prompt repairs, companies can keep their competitive edge, enhance resource appropriation, and ultimately improve their profits through enhanced operational efficiency.
Proficiency in Diagnostics
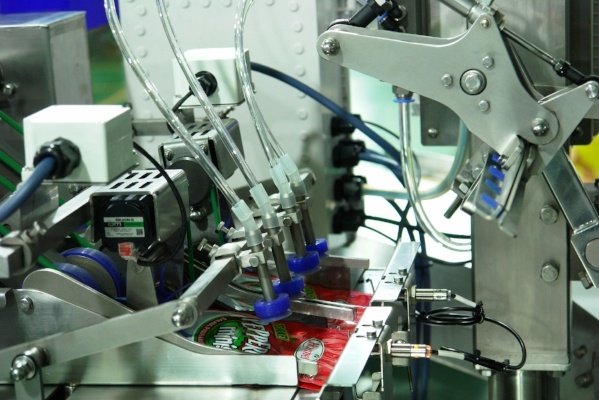
Efficient diagnostics not just help with swift recognition of problems yet additionally enhance the total reliability of packaging procedures. By carrying out comprehensive examinations, specialists can analyze the wellness of crucial components, making sure that even minor irregularities are addressed without delay. This focus to detail lessens the threat of unexpected failures, which can cause pricey downtime.
Additionally, specialist diagnostics offer useful understandings into functional fads, allowing services to make informed choices relating to equipment upgrades or modifications. By leveraging these understandings, firms can enhance their packaging procedures, leading to improved efficiency and efficiency. Inevitably, purchasing analysis expertise is essential for companies looking for to maintain smooth procedures and promote high criteria of top quality in their packaging procedures.
Preventive Upkeep Conveniences
Preventive maintenance complements expert diagnostics by proactively addressing potential issues before they manifest into major issues. By executing a structured precautionary maintenance program, firms can considerably decrease the threat of unforeseen equipment failings, thus minimizing costly downtime. Regular examinations, cleaning, and parts substitute help guarantee that packaging machinery runs at optimal like this efficiency.
One of the essential benefits of preventive maintenance is its capability to expand the life expectancy of devices. By routinely maintaining equipment, services can stay clear of the worsening impacts of wear and tear that typically cause significant repair services or replacements. packaging machine repair service. This not only conserves capital however also boosts the total dependability of production procedures
Furthermore, precautionary maintenance adds to enhanced safety problems within the work environment. By determining and rectifying possible dangers before they rise, companies create a more secure atmosphere for their employees. This aggressive technique not only protects employees but additionally promotes a culture of duty and caution.
Custom-made Service Solutions
Identifying the special demands of each organization, personalized service solutions for packaging device repair offer tailored methods that enhance operational efficiency. These options are developed to deal with particular difficulties dealt with by various markets, ensuring that maker downtime is lessened and efficiency is optimized.
Expert repair work services begin with a comprehensive analysis of a firm's packaging procedures. By comprehending the particular equipment entailed and the needs of the production setting, service technicians can establish a personalized repair and maintenance plan. This may consist of specialized training for in-house staff, the execution of predictive maintenance innovations, or the provision of committed support throughout top manufacturing times.
In addition, tailored options can integrate adaptable service contracts that align with a company's operational timetable, enabling fixings to be performed throughout off-peak hours. By prioritizing the special needs of each service, these custom services make sure that repair work are not just efficient but likewise perfectly incorporate right into existing process.
Ultimately, the concentrate on modification makes it possible for companies to enhance their packaging procedures, you can find out more resulting in boosted integrity and efficiency of machinery, which is essential for maintaining competitive advantage in today's hectic market.

Effect On General Efficiency
Customized service options not just address certain repair needs however additionally play a significant role in improving total functional effectiveness. By giving targeted interventions, specialist product packaging machine repair work solutions directly decrease the frequency and period of equipment failures. This proactive method ensures that assembly line stay functional, reducing interruptions that can result in expensive downtime.
In addition, effective repair work services contribute to smoother process, as well-kept machinery runs at ideal performance levels. When machines work appropriately, the top quality of packaged items enhances, leading to less issues and much less rework. This improvement not only increases productivity yet likewise enhances customer complete satisfaction.
On top of that, routine maintenance and fast action times from repair specialists promote a culture of integrity within the organization. Staff members can focus on their primary tasks instead of bothering with prospective devices malfunctions. Consequently, the total throughput of the manufacturing procedure increases, allowing firms to satisfy demand more properly.
Inevitably, the calculated financial investment in professional repair service services converts to enhanced efficiency across all functional facets, making certain that services can adapt and grow in an open market. This synergy between maintenance and performance is necessary for long-term success.
Conclusion
In final thought, expert product packaging device fixing solutions play an essential role in lessening downtime and improving productivity within producing environments. Timely repair work, professional diagnostics, and preventative upkeep add to the integrity of equipment, while personalized solution options deal with details functional demands Click Here - packaging machine repair service.
Comments on “Top packaging machine repair service to keep your operations on track.”